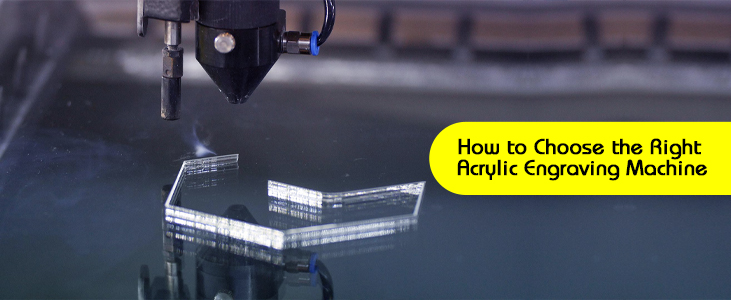
Those of you who have dragged a saw through the edges of an acrylic material know the effort it takes. You know that working as a manual laborer requires a lot of effort as the owner of an acrylic company in Dubai. Traditional methods may take a lot of time, and even worse, you may not succeed. Recent years have seen laser work become very popular. The technology has made its way onto many professionals’ workstations.
Laser engraving machine, however, is not the easiest tools to work with. You need knowledge and experience to function properly if you are new to laser machine as acrylic fabricators in Dubai. Thus, this guide is meant to help you get started as a laser engraver. We will discuss lasers on acrylic sheets in detail in this section along with details on how a wide range of laser cutter and fiber laser can benefit in engraving a variety of materials. In addition, we will discuss acrylic laser cutting in Dubai basics, its mechanism, and its advantages and disadvantages.
The article will hopefully help you gain some courage and go near the beam, which will then allow your business to flourish. Prior to getting started, let’s define what acrylic cutting is and why it has gained popularity.
You can add unique and fascinating features to acrylic materials with acrylic engraving. How so? Drawing virtually any pattern is possible, no matter how simple, complicated, or intricate it is. You’re probably wondering how anything like this could even be possible.
I will walk you through the entire acrylic engraving process, including all the necessary steps.
Let’s get started.
Table of Content
What is Acrylic Engraving?
A fiber laser engraving machine is used to print texts or photographs onto acrylic sheets. A wide variety of designs can be achieved using engraving on acrylic sheets or a wide range of materials. Ideal engraving produces a range of designs through multiple cutting process. Laser engraving machines along with laser tubes and laser systems are used to accomplish this.
The acrylic engraving process will be discussed in more detail later in this guide. Presently, large firms and individuals use laser engravers with acrylics for engraving, as well as those who consider engraving and then pursue it as a hobby. It can be challenging to choose the right type of laser for your marking or engraving project because there are so many types available and you might have to work on thinner or thicker materials.
In order to know where to begin, you must first distinguish between marking and engraving, and then determine what materials you would like to mark or engrave with a laser engraving machine. This article will provide you with an overview of laser marking and engraving machines, along with some tips to consider when choosing one.
Laser marking vs. laser engraving
Both laser marking and engraving are different processes, even if they are often used interchangeably. Laser marking leaves a lasting mark on a surface by using a low-powered laser type. Utilizing material oxidation, you can alter the appearance of the material. It does this without damage to the surface of the material, and the result is a clean, defect-free mark via industrial marking laser.
The high-quality results produced by Epilog Laser machines have made laser cutting acrylic one of the most popular applications for these machines. If you cut acrylic with a laser, you can get a smooth, flame-polished edge, while if you engrave acrylic with a laser, the engraving will be bright and frosty white.
Different types of Acrylics
It’s important to understand the different types of acrylics before beginning to experiment with acrylic in your laser stations. Cast acrylic and extruded acrylic are the two types of acrylic suitable for lasers.
Cast Acrylic:
The liquid acrylic used in casting acrylic sheets is poured into molds that can be customized to take on different shapes and sizes. The majority of awards on the market are made of this type of acrylic. Cast acrylic turns frosty white when engraved, making it the ideal material for engraving. The edges of cast acrylic can be flame-polished, but the acrylic itself cannot be laser-cut. Engraving saves cost of laser cutting and is a better use for cast acrylic.
Extruded acrylic:
Extruded acrylic, which is very popular as a cutting material, is another type of acrylic. Typically, extruded acrylic costs less than cast acrylic, because it is made through higher-volume manufacturing processes, and it behaves differently with a laser beam. The laser-cut edges of extruded acrylic will be flame-polished and will be clean and smooth. As opposed to a frosted look, it will appear clear when it is engraved.
Best Acrylic Engraving Tools for Laser Cutting Acrylic
Cutting extruded acrylic will produce the best results if the material is elevated so that it doesn’t touch the cutting table. After laser cutting, this will greatly reduce the amount of backside reflection and grid marks on the material.
Using Epilog’s Pin Table, you can make those perfect cuts on harder materials in extruded acrylic. For better cutting-edge quality using powerful lasers, you can raise and support your acrylic with this handy tool. In the Pin Table, movable pins are placed along a grid of holes spaced one inch (25.4 mm) apart. The pins can be moved anywhere on the material surface. This means that raised and reinforced areas of the acrylic are not cut by the laser, which helps to eliminate backside reflection.
Alternatively, you can place pins on the Pin Table to support soft materials, small or intricate parts that would normally fall off the cutting pattern.In general, slow speed and high power are the most straightforward process of cutting acrylic. Through this method, the laser beam melts the acrylic edges, giving the acrylic designs and acrylic plate a flame-polished finish.
Cast and extruded acrylics are produced today by a variety of companies that feature a variety of colors, textures, and patterns. Because acrylic offers such a variety of uses, it’s no wonder laser cutters and engravers love it.
Acrylic is generally engraved on the back side so that you can see through it from the front side. Acrylic awards are often engraved this way.
The front and back of acrylic sheets are typically coated with a protective adhesive film to prevent scratching. Ideally, the backing paper should be removed from the acrylic before engraving, while the protective cover should remain on the front to prevent scratching. Remember to mirror or reverse your artwork before sending it to the laser since the backside will be engraved.
In general, acrylic engraves well at a fast speed and with low power. Applying too much power for marking acrylic can lead to develop distortions in the material.
Frequently Asked Questions – (FAQ)
1. What are some tips for processing acrylic with lasers?
If you are working with acrylic, never leave it unattended. Lasers have been shown to create a particularly flammable environment when cutting acrylic, in whatever form it may take. If you are not present when your laser is operating – regardless of the material – you should not use it.
The type of acrylic you use for your application should be considered carefully. Extruded acrylic is best for laser cutting, while cast acrylic is best for engraving.
Remove the backside reflection by elevating the acrylic with Epilog’s Pin Table or another support.
2. Is acrylic suitable for creating any type of project?
Acrylic is an ideal material for laser processing due to its durability and practicality. This material is ideal for many purposes due to its variety of colors and textures:
- Signage at the point of sale
- Signage providing directions
- Pendants/earrings/buttons
- Boxes and containers
- Toppers for cakes and cupcakes
- Awards customized to the recipient
- Decorations for the holidays
- Plus much more!
3. Acrylic plastic lasts for how long?
The fact that an acrylic sheet has UV protection as well as the benefits of high impact resistance and durability means the service life should be able to last ten years or more with proper care.